· Zen HuiFer · Building an Enterprise-level IoT Platform from Scratch · 16 min read
Device Management
This article details various aspects of IoT device management and maintenance, including device registration, device authentication, device monitoring, etc. Through a systematic device management process, ensure that devices operate efficiently and securely throughout their lifecycle.
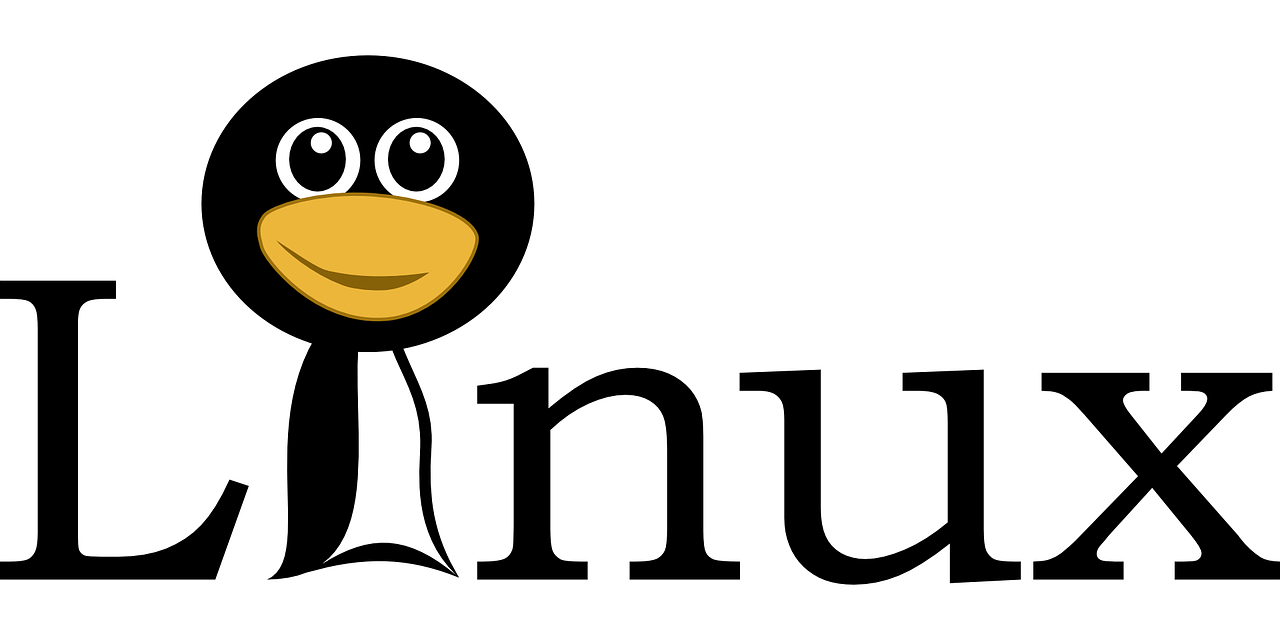
Device Management
Device Registration
Device registration is the first step in IoT device management, ensuring that each device has a unique identifier in the system. The device registration process typically includes the following steps:
- Device Identification: Assign a unique identifier (such as MAC address, serial number, etc.) to each device for tracking and management in the system.
- Device Record: Enter the basic information of the device (such as device type, model, production date, etc.) into the device management system for subsequent management and maintenance.
- Initial Setup: Perform initial configuration on newly registered devices, including network settings, firmware updates, etc., to ensure the device can operate normally.
- Device Grouping: Group devices according to certain rules, such as by geographic location, device type, or function, for batch management and operation.
- Device Tagging: Add tags to devices for quick search and filtering. For example, tags like “high priority” or “needs maintenance” can be added to quickly locate specific devices when there are many devices.
- Device Permission Management: Assign different permission levels to different devices to ensure that only authorized users can operate the devices, enhancing system security.
- Device Documentation Management: Create and maintain relevant documents for each registered device, including user manuals, technical specifications, maintenance guides, etc., for subsequent use and maintenance.
- Device Interoperability Testing: Conduct interoperability testing during the device registration process to ensure that the device can seamlessly cooperate with other devices and platforms in the system.
Device registration is not only the starting point of device management but also the foundation to ensure that devices can operate efficiently and securely throughout their lifecycle. A systematic device registration process can greatly improve the efficiency and accuracy of device management, laying a solid foundation for subsequent device maintenance, monitoring, and updates.
Device Authentication
Device authentication is an important step to ensure device identity and data security. Common device authentication mechanisms include:
- Digital Certificates: Issue digital certificates to each device, and use Public Key Infrastructure (PKI) for identity verification to ensure the legitimacy of the device.
- Key Exchange: Use symmetric or asymmetric encryption technology to exchange keys between the device and the server to ensure the confidentiality and integrity of communication data.
- Two-Factor Authentication: Combine the hardware characteristics of the device with user authentication information (such as passwords, fingerprints, etc.) to improve the security of device authentication.
- Device Fingerprint: Generate a unique device fingerprint based on the hardware characteristics of the device (such as MAC address, serial number, etc.) for device identity verification.
- Dynamic Password: Use dynamic password technology (such as TOTP, HOTP, etc.) for device authentication to ensure the security and timeliness of the authentication process.
Device authentication is not only a security guarantee for device access to the system but also a key link to ensure the security of device data transmission and operation. Through multi-level and diversified authentication mechanisms, unauthorized device access and data leakage can be effectively prevented, enhancing the security and reliability of the entire IoT system.
Authentication Mechanism | Advantages | Disadvantages | Application Scenarios |
---|---|---|---|
Digital Certificates | High security, based on Public Key Infrastructure (PKI) | Requires complex certificate management, high cost | Suitable for scenarios with high-security requirements, such as finance, healthcare, etc. |
Key Exchange | Ensures the confidentiality and integrity of communication data | Requires secure key management, potential risk of key leakage | Suitable for scenarios requiring encrypted communication, such as communication between IoT devices and servers |
Two-Factor Authentication | Improves authentication security, combines hardware characteristics and user authentication information | Complex implementation, may affect user experience | Suitable for scenarios with high-security requirements, such as internal enterprise systems, important device management, etc. |
Device Fingerprint | Generates a unique device fingerprint for device identity verification | Relies on hardware characteristics, potential risk of forgery | Suitable for scenarios requiring unique device identification, such as device registration, device tracking, etc. |
Dynamic Password | Ensures the security and timeliness of the authentication process | Requires additional hardware or software support, may affect user experience | Suitable for scenarios requiring frequent authentication, such as device login, sensitive operations, etc. |
Device Monitoring
Device monitoring is mainly used to monitor the normal condition of the device, including the operating status, data collection, device status, etc.
Health
Device health is an important indicator to evaluate the operating status and performance of IoT devices. By monitoring the health of the device, potential problems can be detected in time, and corresponding maintenance measures can be taken to ensure the normal operation of the device.
The calculation formula for device health is as follows:
The meanings of each parameter are as follows:
- Uptime: The normal operating time of the device, in hours. It indicates the normal working time of the device over a period of time.
- Performance: The performance index of the device, ranging from 0 to 1. It indicates the performance of the device during operation, with 1 being the best performance and 0 being the worst performance.
- ErrorRate: The error rate of the device, ranging from 0 to 1. It indicates the frequency of errors occurring during the operation of the device, with 0 indicating no errors and 1 indicating frequent errors.
- Age: The service life of the device, in years. It indicates the length of time the device has been in use from the time it was put into use to the present.
For example, we have a device with the following parameters:
- Uptime: 720 hours (i.e., the normal operating time of the device in one month)
- Performance: 0.9 (the performance of the device is relatively good)
- ErrorRate: 0.05 (the error rate of the device is relatively low)
- Age: 2 years (the device has been in use for 2 years)
Substitute these parameters into the health calculation formula:
The calculation process is as follows:
- Calculate the product of uptime and performance:
- Calculate the complement of the error rate:
- Calculate the product:
- Finally, divide by the service life of the device:
Therefore, the health of the device is 307.8.
In this way, we can quantitatively assess the health of the device, detect potential problems in time, and perform maintenance.
Operating Status
The operating status of the device refers to the working condition of the device at a certain moment, including whether the device is operating normally, whether there is a fault, the current working mode, etc. By monitoring the operating status of the device, abnormal conditions of the device can be detected in time, and corresponding measures can be taken to deal with them.
The monitoring of the operating status of the device can be carried out in the following ways:
Status Report: The device regularly sends status reports to the server, including the current status of the device, operating parameters, fault information, etc. After receiving the status report, the server can analyze the operating status of the device and determine whether the device is operating normally.
Real-time Monitoring: Through the real-time monitoring system, the operating status of the device is monitored in real-time. The real-time monitoring system can collect the operating data of the device in real-time through sensors, monitoring software, etc., and transmit the data to the monitoring center for analysis.
Fault Alarm: When a fault occurs in the device, the device can send fault alarm information to the administrator through the alarm system. The alarm information can be sent via SMS, email, phone, etc., to ensure that the administrator can receive the fault alarm information in time and take corresponding measures to deal with it.
Remote Diagnosis: Through the remote diagnosis system, the administrator can remotely view the operating status of the device, perform fault diagnosis and troubleshooting. The remote diagnosis system can connect to the device through the network, obtain the operating data of the device, and analyze the data to determine the cause of the fault.
Performance Indicators
Performance indicators are important parameters to evaluate the performance of the device during operation. The following are some common performance indicators:
Throughput: Indicates the number of tasks or data processed by the device per unit time. The higher the throughput, the stronger the processing capacity of the device. The calculation formula is:
Response Time: Indicates the time required for the device to start responding to a request after receiving it. The shorter the response time, the faster the response speed of the device. The calculation formula is:
Utilization: Indicates the usage of the device over a period of time, usually expressed as a percentage. The higher the utilization, the higher the usage efficiency of the device. The calculation formula is:
Latency: Indicates the time required for data to be transmitted from the source to the destination. The lower the latency, the higher the efficiency of data transmission. The calculation formula is:
Error Rate: Indicates the frequency of errors occurring during the processing of tasks or data transmission by the device. The lower the error rate, the higher the reliability of the device. The calculation formula is:
Calculation Indicators
In device management and maintenance, clear calculation indicators help quantify the operating status and health of the device. The following are some common calculation indicators:
Device Health: The calculation formula for device health has been detailed earlier. By calculating the device health, the overall operating status of the device can be assessed.
Mean Time Between Failures (MTBF): Indicates the average operating time between two failures. The longer the MTBF, the higher the reliability of the device. The calculation formula is:
Mean Time To Repair (MTTR): Indicates the average time from the occurrence of a failure to the completion of the repair. The shorter the MTTR, the better the maintainability of the device. The calculation formula is:
Availability: Indicates the proportion of time the device is in a normal operating state over a period of time. The higher the availability, the better the reliability and maintainability of the device. The calculation formula is:
Failure Rate: Indicates the frequency of failures occurring in the device per unit time. The lower the failure rate, the higher the reliability of the device. The calculation formula is:
Specific Cases
To better understand the above concepts, here are some specific cases:
Case 1: Industrial Robot Health Assessment
A factory uses an industrial robot that works 24 hours a day, 30 days a month. After a period of operation, it is found that the robot’s normal operating time per month is 648 hours, the performance coefficient is 0.9, the error rate is 5%, and the service life is 2 years. According to the health calculation formula mentioned earlier, the health of the robot can be calculated:
The calculation shows that the health of the robot is 307.8, indicating that its overall operating condition is good.
Case 2: Server Performance Indicator Monitoring
A company uses a server to handle a large number of network requests. Through the monitoring system, the performance indicators of the server are as follows:
- Throughput: 500 requests per second
- Response Time: Average response time is 200 milliseconds
- Utilization: CPU utilization of the server is 75%
- Latency: Data transmission latency is 50 milliseconds
- Error Rate: 10 errors per million requests
Based on these performance indicators, the processing capacity and reliability of the server can be assessed, and potential problems can be identified and resolved in a timely manner.
Case 3: Device Failure Rate and Maintenance
A manufacturing company uses a critical device that has a total operating time of 8760 hours in the past year, during which 5 failures occurred, and the total repair time was 50 hours. According to the calculation formulas mentioned earlier, the MTBF, MTTR, and failure rate of the device can be calculated:
- Mean Time Between Failures (MTBF):
- Mean Time To Repair (MTTR):
- Failure Rate:
Through these calculation indicators, the reliability and maintainability of the device can be assessed, and corresponding maintenance plans can be formulated.
Case 4: Remote Diagnosis and Troubleshooting
A company has deployed a large number of IoT devices globally. To improve maintenance efficiency, the company introduced a remote diagnosis system. One day, the system detected an abnormal operating status of a device. The administrator viewed the operating data of the device through the remote diagnosis system and found that the temperature sensor of the device was faulty. The administrator sent a command through the remote diagnosis system to restart the temperature sensor, successfully resolving the issue and avoiding losses caused by device downtime.
Equipment Maintenance
Equipment maintenance is an important part of ensuring the normal operation of equipment and extending its service life. Common types of equipment maintenance include preventive maintenance, predictive maintenance, and corrective maintenance. The tasks to be performed under different maintenance categories are shown in the table below:
Maintenance Category | Main Tasks |
---|---|
Preventive Maintenance | - Regularly check the operating status of the equipment, identify potential problems and deal with them in a timely manner - Regularly replace vulnerable parts, such as filters, seals, etc. - Regularly lubricate the moving parts of the equipment to reduce wear - Regularly clean the equipment to keep it clean and hygienic |
Predictive Maintenance | - Use sensors and monitoring equipment to collect real-time operating data of the equipment - Use big data analysis and machine learning technology to analyze the operating data of the equipment and predict fault trends - Develop maintenance plans based on prediction results and perform maintenance in advance |
Corrective Maintenance | - Quickly diagnose the cause of the fault and determine the fault location - Timely replace or repair faulty parts - Conduct a comprehensive inspection of the equipment to ensure that the fault is completely eliminated - Record the fault and repair situation, and summarize the experience and lessons |
To improve the efficiency and effectiveness of equipment maintenance, an equipment maintenance management system can be introduced. The main functions of the equipment maintenance management system include: equipment information management, recording the basic information, operating status, maintenance records, etc. of the equipment; maintenance plan management, formulating and managing the maintenance plans of the equipment to ensure that maintenance work is carried out on time; fault management, recording and analyzing the fault situation of the equipment, and formulating fault handling plans; spare parts management, managing the spare parts inventory of the equipment to ensure timely supply of spare parts.
Equipment Update
Equipment update refers to upgrading or replacing existing equipment to improve its performance, reliability, and safety. The main tasks of equipment update include:
- Evaluate the performance and status of existing equipment to determine whether an update is needed.
- Develop an equipment update plan, including the update time, budget, and resource allocation.
- Select suitable new equipment or upgrade solutions to ensure that the new equipment can meet business needs.
- Install and debug the new equipment to ensure its normal operation.
- Train operators to ensure they can operate the new equipment proficiently.
- Record the process and results of the equipment update as a reference for subsequent maintenance and management.
The purpose of equipment updates is to improve production efficiency, reduce operating costs, and enhance the competitiveness of the enterprise by introducing new technologies and new equipment. When performing equipment updates, it is necessary to comprehensively consider the performance, cost, compatibility, and maintainability of the equipment to ensure that the updated equipment can operate stably for a long time. Therefore, choosing the right equipment update strategy is crucial to meet the actual needs of the enterprise. The following are the advantages and disadvantages of different equipment update strategies:
Update Strategy | Advantages | Disadvantages | Applicable Scenarios |
---|---|---|---|
Comprehensive Update | - Improve overall system performance - Standardize equipment, making it easier to manage - Lower long-term costs | - High initial investment - Complex update process, which may affect production | Suitable for scenarios where equipment is severely aging and overall performance needs to be improved |
Step-by-Step Update | - Disperse investment, reduce initial costs - The update process has less impact on production | - Non-uniform equipment standards, making management complex - Potential compatibility issues between new and old equipment | Suitable for scenarios with limited budget and the need to gradually improve equipment performance |
Key Equipment Update | - Improve the performance and reliability of key links - Relatively small investment, quick results | - Limited overall system performance improvement - Potential system bottlenecks | Suitable for scenarios where key equipment performance bottlenecks are obvious |
Software Upgrade | - Low cost, easy to implement - Improve equipment functions and performance | - Limited hardware performance improvement - Potential compatibility issues | Suitable for scenarios where hardware performance is acceptable but functionality needs to be improved |
Leasing or Outsourcing | - Reduce initial investment - Enjoy the latest technology and equipment | - Higher long-term costs<br- Dependence on external suppliers, less flexibility | Suitable for short-term projects or scenarios with high uncertainty |
Equipment Scrap
Equipment scrap refers to the process of removing equipment that can no longer be used normally or has high maintenance costs from the production system. The main tasks of equipment scrap include:
- Evaluate the status and performance of the equipment to determine whether it needs to be scrapped.
- Develop an equipment scrap plan, including the scrap time, budget, and resource allocation.
- Safely dismantle and remove the scrapped equipment to ensure no impact on the production system.
- Dispose of the scrapped equipment to ensure compliance with environmental and safety regulations.
- Record the process and results of the equipment scrap as a reference for subsequent management.
The equipment scrap process needs to follow certain specifications and procedures to ensure the safety and compliance of the scrap process. The following are the detailed steps of equipment scrap:
- Equipment Status Evaluation: Conduct a comprehensive inspection and evaluation of the equipment to determine its operating status, fault situation, and remaining service life. The evaluation results will be an important basis for equipment scrap decisions.
- Scrap Application and Approval: Based on the evaluation results, fill out the equipment scrap application form, detailing the reasons for scrap, equipment information, and disposal plan. The scrap application needs to be approved by relevant departments to ensure the rationality and compliance of the scrap decision.
- Develop Scrap Plan: After the scrap application is approved, develop a detailed equipment scrap plan, including scrap time, dismantling steps, safety measures, and resource allocation. The scrap plan should consider production arrangements to minimize the impact on production.
- Safe Dismantling and Removal: Safely dismantle and remove the scrapped equipment according to the scrap plan. During the dismantling process, necessary safety measures should be taken to prevent accidents. At the same time, ensure that the dismantling process does not affect other equipment and the production system.
- Environmental Disposal: Dispose of the scrapped equipment in an environmentally friendly manner to ensure compliance with environmental regulations and standards. Options include recycling, harmless treatment, or entrusting professional organizations for disposal to reduce environmental impact.
- Recording and Summary: Record the entire process of equipment scrap in detail, including evaluation results, approval records, dismantling process, and disposal methods. Summarize the scrap experience, analyze the reasons for scrap, and provide a reference for subsequent equipment management and maintenance.
By following a standardized equipment scrap process, the risks in the equipment scrap process can be effectively reduced, ensuring the safety and environmental compliance of the scrap process. At the same time, equipment scrap records and summaries help enterprises optimize equipment management strategies, improve equipment utilization, and production efficiency.